Safety is a crucial consideration when working with electrical circuits and systems. Contractors have to take all the necessary precautions to reduce and even eliminate the risk of electrocution, whether it is when these systems are being installed or when they are in use. Using conduits in these applications remains the best way to eliminate these risks. There are several types of conduits used in structural and building materials. It is important to use the right type of conduit, especially in underground applications. So, what types of conduits are available for these uses?
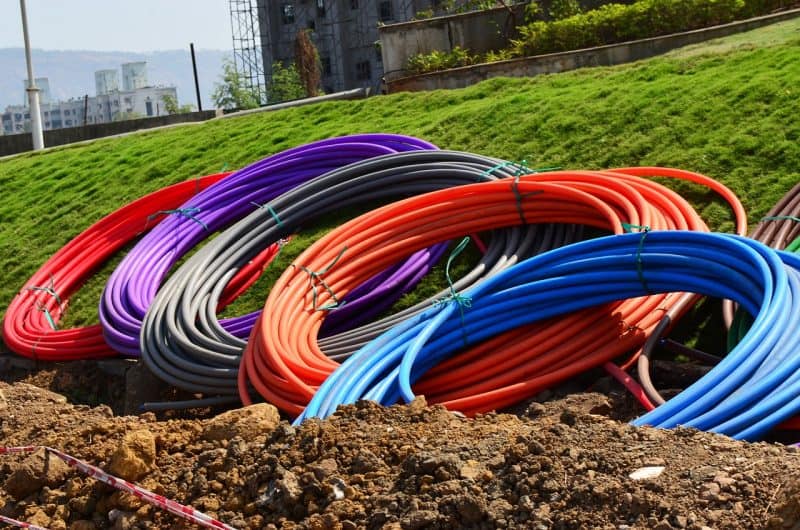
Metal Conduits
These conduits have been used for a long time, and they are typically made of steel or aluminum. They are being phased out, with alternatives like PVC and fiberglass being used instead.
Rigid metal conduits are made of coated steel. Although they provide adequate protection, their weight and thickness make them expensive and harder to handle. They also require threads for all joints, a feature that makes installing wires difficult.
Even though it is not used underground, electrical metal tubing is a lightweight and bendable option for indoor applications. These conduits are used where there is little risk of damage.
Flexible metal conduits are made of helical coiled metal strips that interlock. Although they are bendable, their thick walls make them very challenging to install and use.
Fiberglass Conduits
Fiberglass conduits have become popular over the years because they do not corrode, are affordable and easy to work with, and are resistant to temperature changes, moisture, and chemicals. Fiberglass conduits are now considered the best PVC alternative for rigid conduits that are to be buried underground.
Fiberglass is non-conductive and offers excellent protection for all electrical installations. Additionally, these conduits have a very low friction coefficient which makes it easier to run wires through them.
PVC
PVC conduits are the lightest and cheapest conduit option. They offer excellent protection because they do not conduct electricity. They also come with couplings, connectors, and fittings that make it easier to assemble and join PVC conduits using PVC glue.
They have a serious flaw though in that they cannot withstand hits or pressure very well. They will crack under these conditions, potentially leading to water getting inside and causing a short.
Additionally, they do not do well in places with extreme temperatures. They cannot be installed anywhere where the temperature falls below 20 degrees or rises above 140 degrees Fahrenheit.
Their second serious flaw is that they can catch fire and they produce toxic fumes when they do.
High-Density Polyethylene (HDPE) Conduits
HDPE conduits are easy to install, strong, and flexible. They are mainly used in telecommunications applications and power utility distribution because they offer great protection, ensuring both distribution cables and fiber optic cables are not damaged. They come in reels that are tens or even hundreds of feet long so you can cut the length you need. This means there is no need for threads or joints during their installation.
Although each option discussed above has its pros and cons, we would recommend fiberglass and discourage the use of metal conduits. Using fiberglass conduits means you do not have to worry about things like damage, installation, or even environmental conditions because fiberglass performs well no matter the conditions.
Latest posts by Canadian Home Trends (see all)
- Dining Room Design Tips - August 30, 2025
- Practical Luxury in Forest Grove - August 30, 2025
- The Hidden Value of Great Design - August 30, 2025